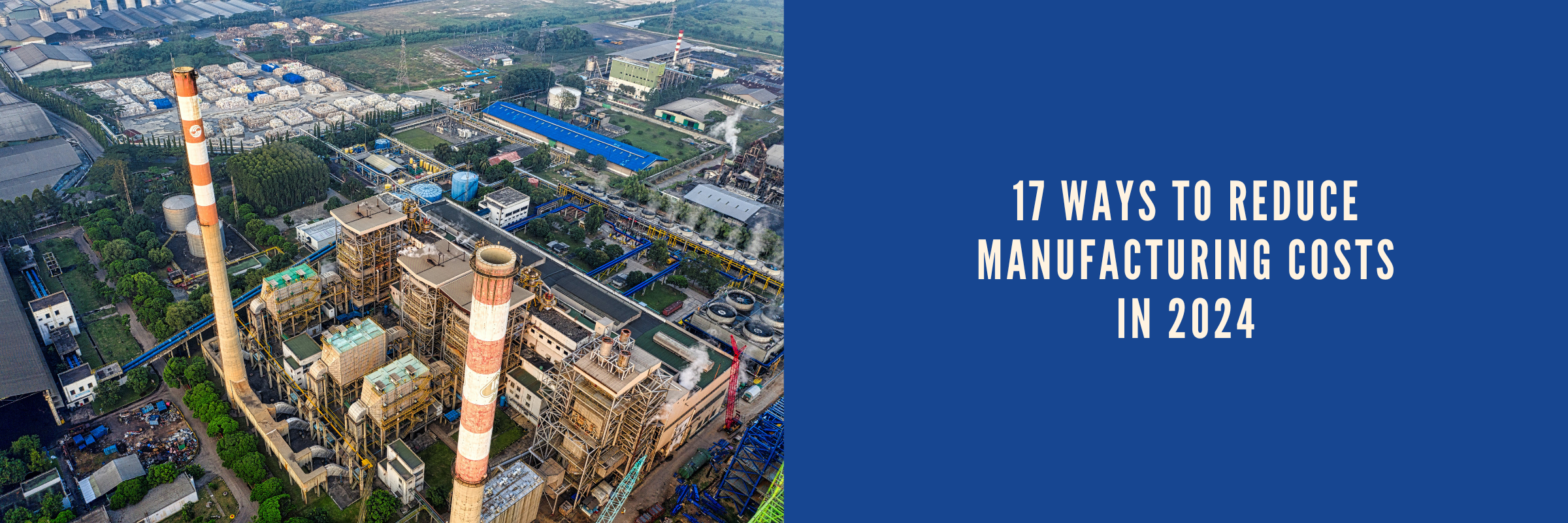
17 Ways To Reduce Manufacturing Costs in 2025
Pranay Agrawal | February 2, 2024 , 7 min read
Table Of Content
Have you ever experienced getting a seemingly lucrative order, only to find that after factoring in all the expenses, there’s hardly any profit left? Almost every manufacturer has encountered this situation at least once, and for some, it’s a regular problem. The main issue? Often, it comes down to the cost of production.
The costs of materials, direct labor, and overheads impact a company’s profitability. That’s why it’s crucial to understand what contributes to these costs and how you can lower them.
This article presents 17 effective strategies, backed by data and focused on results, to help you tackle this challenge head-on.
How To Reduce Manufacturing Costs?
Here are 17 practical ways to reduce manufacturing costs in 2025:
1. Embrace Lean Manufacturing
Implement lean principles to identify and eliminate waste in your production processes. Streamline workflows, optimize resource utilization, and continuously assess and refine your operations to enhance overall efficiency.
The lean principles involve constantly striving to cut out any unnecessary steps or resources in the manufacturing process. Waste in this context can mean various things like time, materials, labor, or inefficient planning. Lean Manufacturing identifies eight types of waste: over/under production, waiting, unnecessary transportation, over/under processing, excess inventory, unnecessary motion, defects, and unused creativity of team members.
The aim of lean is to create value in the most efficient and safe way possible. This is done by respecting people, creating value, reducing waste, focusing on smooth processes, continuously improving, and optimizing the entire system.
2. Invest in Advanced Automation
Explore and invest in automation technologies that can replace manual or repetitive tasks. Automated processes not only reduce labor costs but also minimize errors, increase production speed, and enhance overall precision.
This involves using technology to automate manual, repeatable tasks that were historically performed by humans. There are many ways to do this, like using manufacturing management software or robots to make things faster and with fewer mistakes when making physical products.
Automated processes can reduce labor costs, minimize errors, increase production speed, and enhance overall precision. Automation can also improve efficiency, reduce costs, and increase scalability.
The different types of automation in manufacturing include computer-integrated manufacturing (CIM), the use of robots, and the automation of data capture to improve the efficiency of information and provide insights. By automating some business tasks, companies can free up workers to do more cognitively intensive tasks.
3. Optimize Supply Chain Management
Efficient supply chain management is crucial for cost reduction. Negotiate favorable terms with suppliers, minimize lead times, and streamline procurement processes to ensure timely and cost-effective access to raw materials.
To achieve this, businesses can negotiate favorable terms with suppliers, minimize lead times, and streamline procurement processes to ensure timely and cost-effective access to raw materials. Supply chain efficiency involves shorter order processing times, better inventory management, and faster delivery, which often means higher profitability
4. Adopt Sustainable Practices
Embrace sustainable practices such as renewable energy sources, waste reduction, and eco-friendly materials. Beyond cost reduction, these practices contribute to environmental responsibility and long-term operational savings.
5. Maximize Equipment Utilization
Regular maintenance and proper utilization of machinery can significantly extend their lifespan, reducing the need for frequent replacements and repairs. This proactive approach aids in substantial long-term cost savings.
6. Invest in Employee Training
A well-trained workforce is more efficient and productive. Provide ongoing training to your staff to ensure they are up-to-date with the latest industry trends and technologies, contributing to overall operational excellence.
7. Utilize Predictive Maintenance
Shift from reactive to proactive maintenance by implementing predictive maintenance techniques. Regularly monitor and analyze equipment performance data to identify potential issues before they lead to costly downtime. This not only reduces maintenance costs but also extends the lifespan of machinery.
Predictive maintenance techniques include various methods such as vibration analysis, acoustic analysis monitoring, oil analysis, and infrared thermography analysis, which involve the use of sensors and data analytics to forecast when maintenance will be needed and avoid costly situations.
8. Leverage Business Intelligence through Data Analytics
Manufacturing businesses can harness the power of business intelligence by analyzing production data to further reduce costs. This provides valuable insights into areas for improvement, cost-saving opportunities, and overall operational efficiency.
BI enables the automation of various tasks, leading to reduced labor, and costs, while also providing real-time data and actionable insights for data-driven decision-making. This is an area ScaleupAlly excels. Learn more by taking a look at our case studies.
9. Implement Energy-Efficient Technologies
Explore and adopt energy-efficient technologies, from LED lighting to energy-efficient machinery. This not only contributes to environmental sustainability but also results in significant cost savings.
10. Negotiate Volume Discounts with Suppliers
Establish strong relationships with suppliers and negotiate volume discounts for bulk purchases. This strategic approach can lead to considerable cost savings on raw materials and components.
11. Cross-Train Employees
Foster a flexible workforce by cross-training employees across various roles. This ensures adaptability to changing demands without the need for additional hires, ultimately reducing labor costs.
12. Embrace Circular Economy Practices
Transition towards a circular economy model by reusing materials, refurbishing products, and minimizing waste. This not only aligns with environmental responsibility but also creates a more sustainable and cost-effective production cycle.
13. Conduct Regular Cost Audits
Regularly assess and audit your production costs to identify areas where expenses can be trimmed. This ongoing evaluation ensures that your cost-saving strategies remain aligned with the evolving needs of your business.
14. Explore Outsourcing Opportunities
Evaluate non-core functions within your production process that could be outsourced to specialized service providers. Outsourcing certain tasks can lead to cost reductions and allow your team to focus on core competencies.
15. Implement Just-In-Time Inventory Management
Adopt a just-in-time inventory management system to minimize excess stock, reducing carrying costs and the risk of obsolete inventory. This streamlined approach ensures that materials are procured precisely when needed.
16. Monitor and Optimize Production Processes
Regularly monitor and analyze production processes to identify bottlenecks and inefficiencies. Implementing continuous improvement initiatives based on data-driven insights can result in enhanced productivity and reduced costs.
17. Embrace Digitalization for Efficiency
Incorporate digital tools and technologies to enhance overall operational efficiency. From predictive analytics to real-time monitoring, digitalization can optimize processes, reduce errors, and lead to substantial cost savings.
Conclusion
In summary, cutting manufacturing expenses is not just a savvy business decision but also a vital one for staying ahead in the market and securing lasting prosperity. By using lean manufacturing methods, making the most of labor and energy, and reducing waste, companies can boost profits and support sustainability.
Technology and automation play crucial roles in making operations more efficient. In addition, ScaleupAlly offers combined services to help businesses save money on manufacturing, by using business intelligence tools to build solutions to the manufacturing industry.
Frequently Asked Questions
Q: How can adopting sustainable practices specifically reduce manufacturing costs?
Sustainable practices, such as using eco-friendly materials and renewable energy sources, contribute to cost reduction by minimizing waste, energy consumption, and long-term operational expenses. In addition, companies often find cost efficiencies in recycling and reusing materials within a circular economy model.
Q: Are there specific digital tools recommended for optimizing production processes?
Absolutely. Digital tools such as Manufacturing Execution Systems (MES), predictive analytics software, and real-time monitoring solutions can significantly optimize production processes. These tools enhance efficiency, reduce errors, and contribute to cost savings by streamlining operations.
Q: Can you elaborate on how the just-in-time inventory management system works?
Just-in-time (JIT) inventory management involves ordering and receiving inventory only when it’s needed for production, minimizing excess stock. This system reduces carrying costs and the risk of obsolete inventory. Successful implementation requires close coordination with suppliers and efficient production planning.
Related Blogs
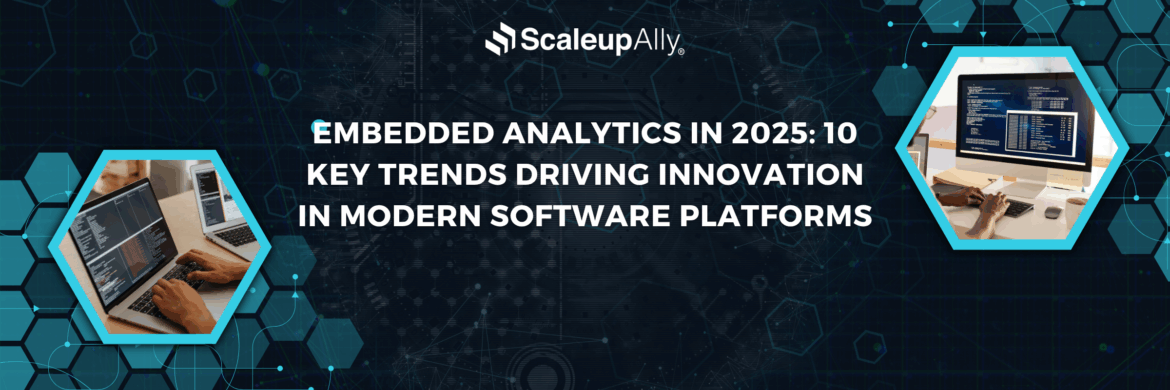
Embedded Analytics in 2025: 10 Key Trends Driving Innovation in Modern Software Platforms
Explore key embedded analytics market trends, growth drivers, tech shifts, and future insights shaping 2025 and beyond in this comprehensive overview.
Tarsem Singh
Jul 31 ,
8 min read
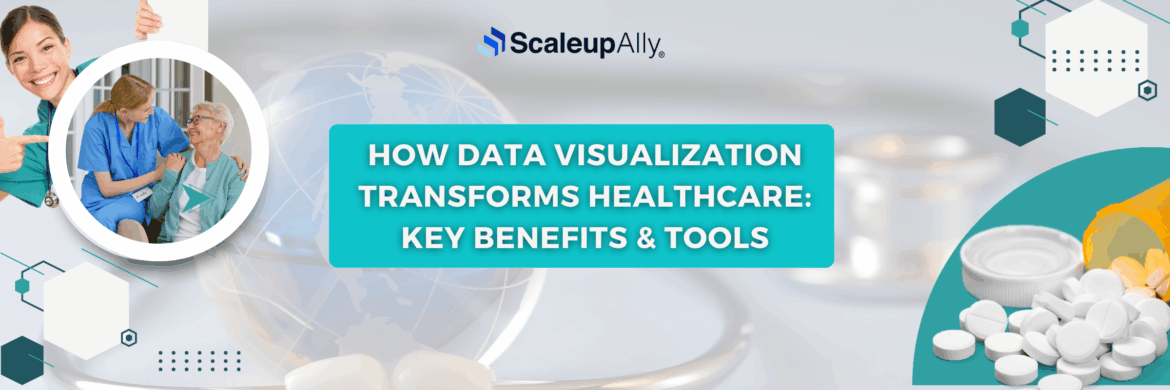
How Data Visualization Transforms Healthcare: Key Benefits & Tools
Explore data visualization in healthcare—its benefits, use cases, and tools that enhance patient care, decision-making, and operational efficiency.
Tarsem Singh
Jul 31 ,
9 min read
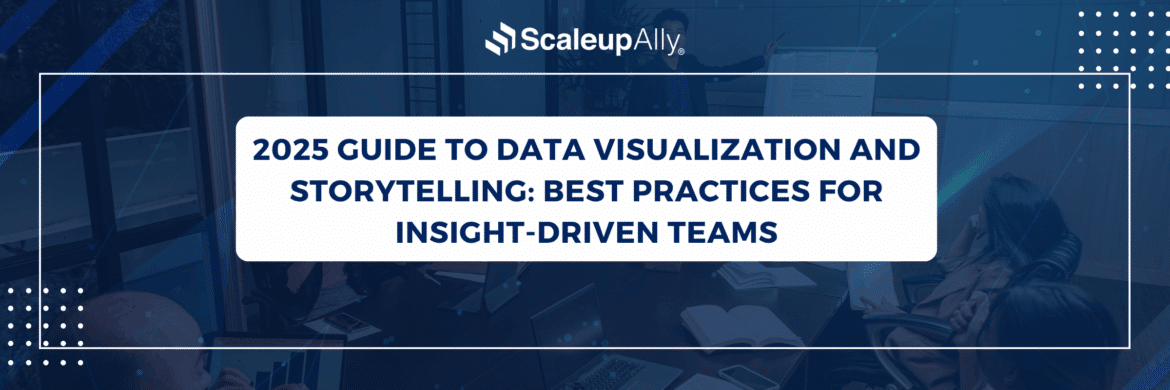
2025 Guide to Data Visualization and Storytelling: Best Practices for Insight-Driven Teams
Master data storytelling with visuals. Learn key elements, differences, best practices, and real-world examples to turn data into compelling narratives.
Tarsem Singh
Jul 31 ,
11 min read