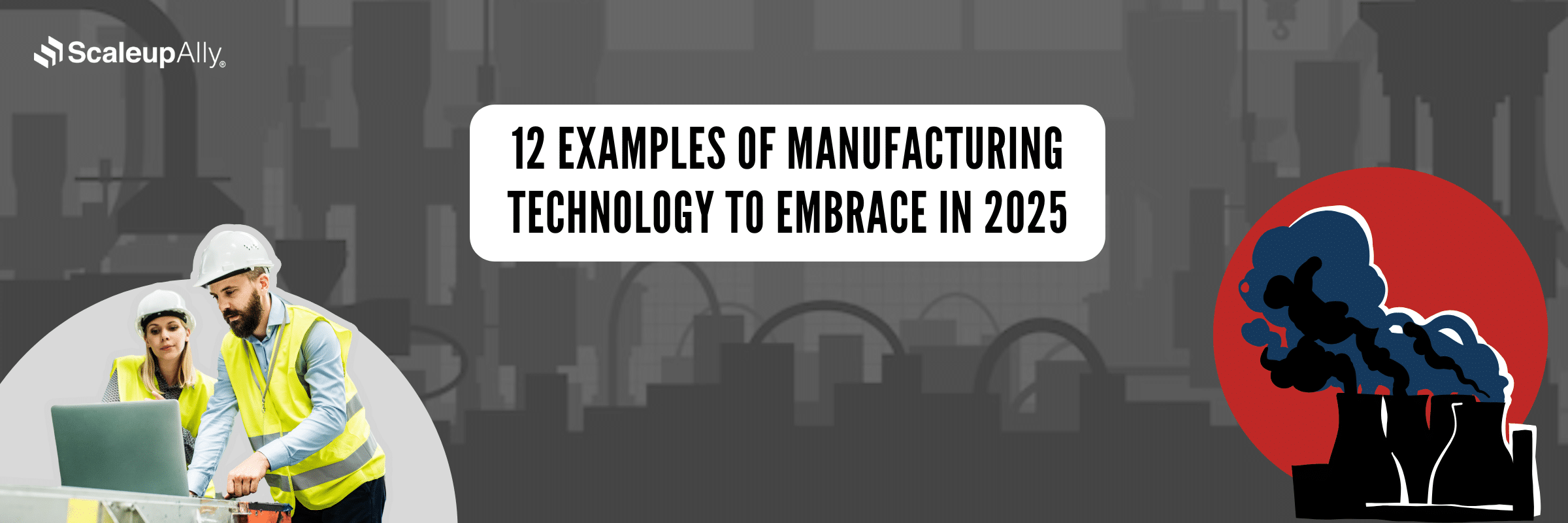
15 Examples of Manufacturing Technology To Embrace in 2025
Suprabhat Sen | March 3, 2025 , 19 min read
Table Of Content
Technology has been at the forefront of manufacturing innovations since the Industrial Revolution, which will likely not change anytime soon. Advancements in technology are progressing at a much quicker pace than before.
Manufacturers are therefore pushed to adapt quickly or risk being left behind. As progress continues, the question is no longer, “Should we adapt?” but rather, “How quickly can we adapt?”
In this blog, we’ll discuss 15 manufacturing technology examples you must embrace in 2025 and the years to come to improve your manufacturing processes.
Key Takeaways
- Industries like aerospace, automotive, healthcare, and energy are leveraging manufacturing technologies to improve efficiency, precision, and sustainability.
- Technologies like AI, 3D printing, and robotics are revolutionizing design, production, and quality control processes.
- Data-driven tools like IoT, ETL, and BI enable real-time monitoring, predictive maintenance, and informed decision-making.
- Simulation technologies like digital twins and machine vision optimize designs, improve processes, and enhance quality assurance.
- While initial costs for adoption are high, these technologies deliver long-term gains in productivity, cost savings, and innovation.
- Cybersecurity is essential to protect digital manufacturing processes and safeguard sensitive data from growing cyber threats.
Key Industries That Can Leverage Manufacturing Technologies
Let’s talk about how manufacturing technologies are reshaping different industries—making everything faster, smarter, and more efficient.
- Aerospace: Imagine aircraft parts being assembled with pinpoint accuracy using automation, cutting down errors. AI is behind lightweight, stronger materials, and engineers use digital twins to test and perfect designs before even building prototypes. Saves time and effort, right?
- Heavy Equipment: Big machines get smarter with IoT sensors that track performance and flag issues before they cause downtime. It’s like giving these machines a way to tell you they need maintenance, saving money and boosting efficiency.
- Automotive: Car manufacturing is a whole new ballgame. Robots and AI make assembly lines faster and more precise, cutting costs while maintaining quality. AI also helps design safer, fuel-efficient cars, and 3D printing makes prototyping and custom parts super easy.
- Consumer Packaged Goods (CPG): Packaging innovation is on fire with 3D printing. Plus, smart packaging—think QR codes and augmented reality—makes products more interactive. And it’s all moving toward eco-friendly processes to reduce waste.
- Healthcare: Custom prosthetics and implants? Thank 3D printing. Robotics take surgeries to the next level with more precision, and AI is like a detective for medical images, improving diagnostics and patient care.
- Electronics: Tiny gadgets need big precision. Advanced manufacturing nails it, while AI spots defects to ensure reliability. And when you need prototypes? Just print them in 3D.
- Energy: From building wind turbines to maintaining solar panels, robotics have got it covered. AI optimizes energy grids and forecasts demand, while new materials improve efficiency and sustainability.
15 Top Manufacturing Technology Examples
Steam propelled the original Industrial Revolution; electricity powered the second; preliminary automation and machinery engineered the third; and cyber physical systems, or intelligent computers, are shaping the Fourth Industrial Revolution.
Let’s take a look at some of these technologies used in manufacturing.
1. Business Intelligence (BI)
Business Intelligence is an umbrella term that includes best practices, software, infrastructure, and other tools to improve decision-making and enhance a business’s performance. In essence, BI uses tools to analyse data for business decision-making. It gathers data from multiple sources and provides insights that increase productivity and improve operations.
Benefits of Using Business Intelligence
- Provides real-time data for faster, more informed decisions.
- Automates reporting and analysis, saving time and resources.
- Identifies areas where expenses can be cut without affecting production quality.
- Tracks raw material levels and product demand to prevent overstocking or stockouts.
Application of Business Intelligence
- Use BI dashboards to monitor production lines and worker output in real-time to adjust schedules to avoid delays
- Analyze product demand patterns, adjust stock levels, and reorder materials in advance to prevent production delays.
- Use BI to track material costs and labor expenses to negotiate better rates with suppliers and reduce labor inefficiencies.
- Analyze equipment data to predict potential failures and schedule maintenance, reducing costly downtime and extending equipment life.
- Track and analyze production quality in real-time, identifying defects and ensuring products meet standards.
- Collect data from sensors on equipment. The system sends an alert when machines risk failing, allowing maintenance before breakdowns occur.
Cost Implications
- BI tools range from affordable cloud-based solutions to very expensive customised platforms. The level of customisation and features you require will determine the actual cost.
- Range: US$30,000 – US$250,000 (depending on the size of the organization and scope of BI).
2. Generative AI
Generative AI is one of today’s hottest business topics, with companies exploring its potential applications and benefits across industries and functions, including manufacturing. Generative AI refers to using AI to generate designs, prototypes, or simulations. It helps automate certain tasks, making production more efficient and innovative.
Benefits of Using Generative AI
- It speeds up the design and development phase, reducing time-to-market by automating design iterations.
- Generative AI allows manufacturers to easily create personalized or unique product variations based on customer preferences.
- AI suggests process improvements, leading to more efficient manufacturing operations by analyzing data.
Application of Generative AI
- Generative AI produces multiple design variations based on performance criteria, helping manufacturers select the most efficient and functional option.
- Integrated with 3D printing, Generative AI enables the creation of complex, lightweight parts that traditional methods can’t achieve.
- Generative AI allows for highly customized designs, tailoring products to individual customer needs without increasing complexity.
Cost Implications
- Implementing generative AI can be expensive initially, requiring investment in AI tools and training. However, over time, it can lead to cost savings by speeding up the design process and reducing waste.
- Range: US$20,000 – US$200,000 (depending on the complexity of the AI applications and the size of the manufacturing operation).
3. ETL (Extract, Transform, Load)
Many manufacturers today want to use data to guide their decisions but need help managing their growing data sources. More importantly, when they can’t transform their raw data into usable formats, they may have poor data availability, which can hinder the development of a data culture.
ETL is a process that involves extracting data from multiple sources, transforming these data, and loading it into a centralised database. This method is critical for analysing large amounts of data in the manufacturing industry.
Also Read: Why Small Businesses Fear ETL: Insights from Our CMO (Pranay Agrawal)
Benefits of Using ETL
- Combines data from multiple sources (production, supply chain, inventory, etc.) into a unified view, making it easier for decision-makers to analyse.
- Cleanses and standardises raw data, ensuring accurate and consistent information is used in reporting and analytics.
- Provides comprehensive and timely data for real-time analysis, helping manufacturers make informed decisions.
Application of ETL
- Use ETL processes to integrate data from suppliers, warehouses, and logistics systems. This ensures real-time visibility of parts and materials, improves inventory management, and minimizes supply chain delays.
- Use ETL processes to aggregate financial data across multiple departments, standardizing and transforming it for financial reporting and compliance with industry regulations.
Cost implication
- ETL systems require investment in software and possibly custom development to integrate with existing systems. Maintenance over time should also be factored in.
- Range: US$50,000-300,000 (depending on the size of the company, number of data sources, and complexity of the ETL process).
4. 3D Printing
3D printing is not just another technology fad. It is being used widely across the engineering, automotive, and manufacturing industries as a rapid development prototyping tool and, increasingly, for producing final parts.
Benefits of Using 3D Printing
- Reduce costs by producing prototypes and small batches without expensive molds.
- Reduces material waste compared to traditional manufacturing.
- Enables on-demand production of custom parts for specific requirements.
- Supports mass customization without significant cost increases.
- Complex designs that are difficult to create using traditional methods can be done through 3D Printing.
- Shortens production timelines by eliminating the need for molds or tooling.
Application of 3D Printing
- 3D printing creates lightweight components, reducing aircraft weight and improving fuel efficiency. Parts like brackets and ducts are printed on-demand, minimizing inventory costs.
- Use 3D printing to create patient-specific implants and prosthetics.
- Print parts as needed, reducing the need for large inventories and minimizing waste.
- Quickly create replacement parts, reducing downtime and supply chain delays.
Cost Implications
- The cost of 3D printing will depend on the type of materials used and the complexity of the object. It is costly to set up, but the technology often leads to lower overall production costs.
- Range: US$50,000 – US$600,000 (depending on the scale of implementation and technology used).
5. IoT
IoT involves connecting devices and machines to the Internet to share and collect data. In manufacturing, IoT helps track the performance of machinery and supply chain management and makes operations more efficient.
Benefits of using IoT
- IoT sensors monitor machinery in real-time, detecting issues early to prevent breakdowns and reduce downtime.
- Sensors can detect unsafe conditions on the factory floor and trigger alerts to prevent accidents.
- Track production performance and equipment health in real-time, enabling faster response to issues.
- IoT devices monitor energy usage to reduce energy costs and improve sustainability.
Application of IoT
- Track inventory and monitor vending machine status, ensuring products are stocked and reducing spoilage.
- Monitor temperature and humidity during food production, ensuring products meet safety and quality standards.
- Sensors monitor production lines to detect defects and ensure product consistency, reducing waste and improving overall quality.
- Monitor energy consumption in manufacturing plants, optimizing usage and reducing costs.
Cost Implications
- The cost of setting up an IoT will depend on the number of devices you need connected and the complexity of the network. The initial setup might be hefty, but considering the long-term benefits, the price may be worth it.
- Range: US$20,000 – US$500,000 (depending on the scale of implementation and technology used).
6. Robotics
Robotics is one of the best examples of manufacturing technology that has been used for some time now. Robots have been the focus of science fiction and literature, but it wasn’t until recent decades that they became a part of our workforce. Today, they are making their mark in various industries, especially manufacturing. There are various robot and automated integration applications, from food packaging and medical device production to consumer goods assembly and metal fabrication.
Benefits of Using Robotics
- Robots can operate continuously without breaks, significantly boosting output.
- They perform tasks faster than human workers, increasing overall efficiency.
- Robots provide consistent quality with minimal errors, reducing defects.
- Reduces labor costs by automating repetitive tasks.
- Robots can handle dangerous tasks, reducing the risk of injury.
- Easily reprogrammed for different tasks or products, accommodating changes in production.
Application of Robotics
- Use robots for vehicle assembly and painting to enhance speed, consistency, and quality.
- Robots automate sorting and packing in food packaging lines, enhancing efficiency and safety.
- Robotics automates complex welding processes, improving quality and reducing cycle times.
Cost Implications
- It can be quite expensive to purchase and set up robotic systems. However, the potential savings in reduced labor costs and increased productivity make up for it. When implementing robotics in manufacturing, consider maintenance and training as part of the costs.
- Range: US$100,000 – 1 Million USD (depending on the scale and complexity of implementation).
7. Autonomous Vehicles (AGVs)
These are machines used to transport materials across factories without human intervention. Their primary functions include material transport, product handling, and workflow optimization. They are engineered to reduce human labor, improve efficiency, and ensure the seamless movement of goods in diverse settings.
Benefits of Using AGVs
- AGVs operate continuously, reducing the time spent on manual transportation tasks.
- Reduces labor costs by minimizing the need for human operators.
- AGVs can navigate without human intervention, reducing the risk of accidents.
- Provides consistent and accurate material transport reducing errors.
- Operate around the clock without fatigue, increasing productivity
Application of AGVs
- Move components between assembly stations, ensuring a smooth flow of materials and reducing production delays.
- They transport parts to and from assembly lines, ensuring a smooth flow of materials and reducing bottlenecks.
- Use AVGs to transport and handle heavy or sensitive equipment on the factory floor to minimise workplace accidents and improve safety.
Cost implications
- It costs a lot to purchase and integrate autonomous vehicles with the factory’s systems.
- Range: US$100,000-500,000 (depending on the number of AGVs and facility requirements).
8. Cybersecurity
A survey by Make UK revealed that nearly half of British manufacturers faced cyber-attacks last year. A quarter of these companies suffered losses between £50,000 and £250,000.
Beyond financial losses, 65% experienced production downtime, and 43% saw damage to their reputation. As manufacturing processes become more digital, protecting machinery and devices from cyber threats is crucial. Cybersecurity safeguards machines, networks, and data to ensure smooth operations.
Benefits of Using Cybersecurity
- Safeguards proprietary information, trade secrets, and intellectual property.
- Prevents data breaches that could compromise business operations.
- Identifies vulnerabilities and strengthens defenses against cyber threats.
- Helps manufacturers meet industry regulations and standards (e.g., ISO, GDPR).
Application of Cybersecurity
- Protect ICS: Safeguard Industrial Control Systems from unauthorized access and cyber threats.
- Secure Data Exchanges: Protect sensitive information shared with suppliers to prevent breaches.
- Safeguard Remote Monitoring: Ensure secure access and data integrity for remote monitoring systems.
Cost implications
- The cost of acquiring cybersecurity services will largely depend on the complexity of the products being protected. Regular software updates, staff training, and security infrastructure are also added up.
- Range: US$30,000-400,000 (depending on the size of the organisation and the cybersecurity measures implemented).
9. Cloud Computing
Cloud computing has rapidly gained traction, especially since the pandemic. For the manufacturing industry, it offers several key benefits. Manufacturers can reduce IT costs, enhance resource capacity, and boost collaboration among teams by accessing data and applications online rather than relying on local servers. This shift not only streamlines operations but also positions manufacturers to respond quickly to market demands.
Benefits of Using Cloud Computing
- Reduces the need for expensive on-site infrastructure and hardware.
- Operates on a pay-as-you-go model, allowing companies to scale resources based on demand.
- Provides flexibility in accessing data and applications from anywhere, allowing for more efficient remote work and real-time decision-making.
Application of Cloud Computing
- Enable remote monitoring and control of factory operations through cloud computing, allowing engineers to monitor machine performance from any location and make adjustments in real-time.
- Collaborating on product designs in real-time with teams across the globe
Cost Implications
- Cloud computing services are typically subscription-based. You pay based on usage and storage needs. An added benefit is that there is no need for expensive hardware. Long-term cloud costs should be monitored.
- Range: US$50,000-300,000 (depending on the scale of adoption, data volume, and cloud services required).
10. Artificial Intelligence
AI, or artificial intelligence, refers to intelligent systems that can perform tasks and make decisions that typically require human intelligence. It involves using algorithms and advanced technologies to enable machines to learn from data, recognise patterns, reason, and solve problems. AI in manufacturing helps analyse data, improve decision-making, and predict machine failures. It plays a key role in enhancing overall operational efficiency.
Benefits of Using AI
- Automates repetitive tasks, reducing human error and improving speed.
- Monitors machinery in real-time and predicts when maintenance is needed, reducing unexpected downtime.
- Uses AI-powered vision systems to detect defects on the production line, ensuring higher product quality.
- Analyses historical data and market trends to accurately predict demand, helping to avoid overproduction or stock shortages.
Application of AI
- Use AI-driven robotic arms for assembling car parts, improving precision and speed while reducing human error.
- Automating quality control processes using image recognition.
- Employ AI to monitor machine health across production plants, using real-time data analytics to predict potential breakdowns, reducing maintenance costs.
- Use AI-powered cameras to inspect products on the production line. These cameras detect defects the human eye might miss, resulting in higher product quality and reduced rework.
Cost implication
- The cost of integrating AI includes infrastructure purchases, employee training, software, and more. It doesn’t come cheap, but the long-term benefits outweigh the upfront costs.
- Range: U$100,000-800,000 (depending on the scale and complexity of AI adoption in the manufacturing process).
11. Digital Twins
A digital twin is a virtual replica of a physical product, system, or process. In manufacturing, it allows businesses to simulate real-world conditions and improve some processes by using real-time data.
Benefits of Using Digital Twins
- Digital twins enable virtual testing of designs, speeding up innovation and lowering prototyping costs.
- Workers can practice in a risk-free virtual environment before handling real equipment.
- Continuous data from digital twins allows manufacturers to track equipment performance and quickly identify issues.
Application of Digital Twins
- Create and test digital prototypes to refine designs and materials, reducing costs and expediting development.
- Compare real-time production data with virtual models to maintain consistent product standards.
- Optimize space and workflow by simulating factory layouts and testing new configurations without disrupting operations.
Cost Implications
- The initial setup of digital twins can be costly due to the need for advanced software and sensors. However, the technology can lead to significant savings through improved efficiency and reduced downtime.
- Range: $115,000 to $700,000 (depending on the complexity of the manufacturing operation, equipment, and software required).
12. Artificial Vision (Machine Vision)
Artificial vision uses cameras, sensors, and image processing algorithms to allow machines to “see” and interpret their surroundings. It is commonly used in manufacturing for quality control, inspection, and automation.
Benefits of Using Artificial Vision
- Enhances quality control by detecting defects that are invisible to the human eye
- Increases production speed by automating visual inspections
- Reduces human error in visual-based tasks
Application of Artificial Vision
- Inspecting products for defects or irregularities during manufacturing
- Guiding robots in assembly lines for precise operations
- Automating measurement and alignment tasks in production
Cost Implications
- The cost of implementing artificial vision systems depends on the complexity and scale of the solution. High-resolution cameras, sensors, and advanced software can be expensive initially, but the technology leads to long-term savings by improving quality control and reducing the need for manual inspections.
- Range: US$30,000-250,000 (depending on the complexity of the machine vision system and the scale of the manufacturing operation).
13. Augmented Reality (AR)
Augmented Reality overlays digital visuals and information onto the real world using devices like AR glasses or mobile apps. It enhances how workers interact with machines, data, and instructions in real time.
Benefits of Using AR:
- Improves training with immersive, hands-on experiences.
- Increases efficiency by providing real-time guidance.
- Reduces errors with step-by-step visual instructions.
Application of AR:
- Worker training and onboarding.
- Maintenance and repair with guided visuals.
- Assembly line support for complex tasks.
Cost Implications:
- Basic AR solutions: $5,000–$10,000.
- Advanced AR systems: $50,000+ (including hardware, software, and support).
14. Simulation Software
Simulation software creates digital models of manufacturing processes to predict outcomes, test designs, and optimize operations before implementation.
Benefits of Simulation Software:
- Identifies inefficiencies and bottlenecks before production.
- Reduces costs by avoiding trial-and-error on physical machines.
- Improves product design and performance.
Application of Simulation Software:
- Process optimization for assembly lines.
- Product testing and prototyping.
- Facility layout and capacity planning.
Cost Implications:
- Basic simulation tools: $5,000–$15,000/year.
- High-end simulation platforms: $50,000–$100,000+ (based on scale).
15. Smart Manufacturing Platforms
Smart manufacturing platforms connect machines, sensors, and software to create an intelligent ecosystem for real-time monitoring, automation, and decision-making.
Benefits of Smart Manufacturing Platforms:
- Enables predictive maintenance and reduces downtime.
- Optimizes production schedules with real-time data.
- Enhances traceability and quality control.
Application of Smart Manufacturing Platforms:
- Smart factories and IoT-driven manufacturing.
- Supply chain integration and inventory management.
- Energy monitoring and sustainability efforts.
Cost Implications:
- Small-scale systems: $10,000–$30,000/year.
- Large-scale platforms: $100,000+ (depending on complexity).
Transform Your Manufacturing Operations With ScaleupAlly
At ScaleupAlly, we help manufacturers worldwide optimize their processes with technology. Our partnerships boost productivity, performance, speed, and safety.
We integrate systems like Business Intelligence for data insights and use generative AI to enhance product designs. Our ETL processes efficiently gather and transform manufacturing data.
With over six years of experience, we specialize in technology-driven maintenance, including machine health monitoring and data analytics, to extend equipment life and maximize uptime.
Ready to elevate your manufacturing? Book a 30-minute free consultation with our BI expert today!
Conclusion
Your choice of manufacturing technology will depend on your specific needs, but one thing you can’t overlook is the power of data. Data reveals where you’re excelling and where improvements are needed. Analyzing this data helps identify the steps to fix issues in your processes.
Regardless of your chosen technology, integrating data analysis tools in manufacturing processes is essential. They go hand in hand, and without optimizing your data, you may not fully realize the benefits of modern-age technologies.
Frequently Asked Questions
Q: What is meant by manufacturing technology?
Manufacturing technology encompasses various tools and systems to design, produce, and maintain products. It includes machinery, software, and processes that enhance production efficiency, quality, and innovation.
Q: What is the latest technology in manufacturing?
The latest manufacturing technologies include robotics, artificial intelligence, IoT, 3D printing, and business intelligence. These innovative technologies improve efficiency and enable more flexible and customized production processes.
Q: What are the 4 types of manufacturing technologies?
The four main types of manufacturing technologies are additive manufacturing (3D printing), subtractive manufacturing (machining), formative manufacturing (casting, molding), and joining processes (welding, fastening). Each serves different production needs.
Q: What is advanced manufacturing technology with an example?
Advanced manufacturing technology uses innovative tools like robotics, AI, IoT, and 3D printing to boost efficiency, precision, and quality. For example, 3D printing creates customized parts layer by layer, ideal for making lightweight aerospace components or custom healthcare implants, while reducing waste and streamlining production.
References:
- Cyber Security in Manufacturing | Make UK: https://www.makeuk.org/insights/reports/cyber-security-in-manufacturing
Related Blogs
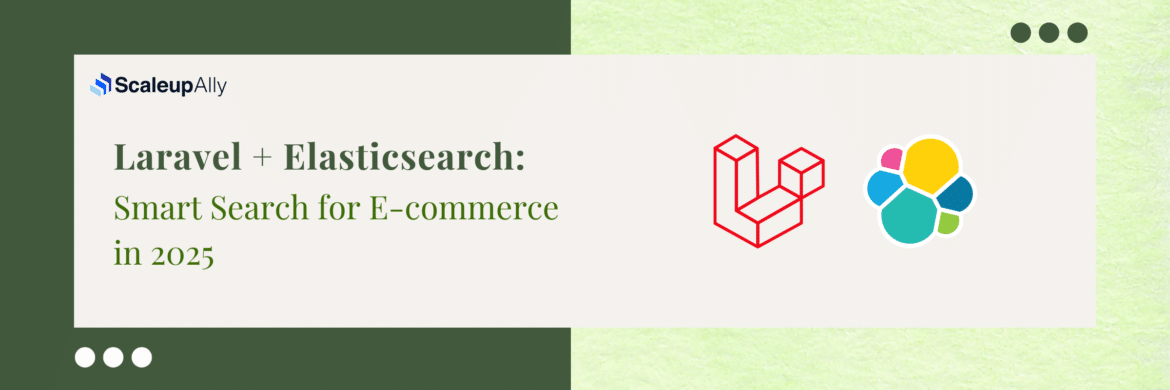
Laravel + Elasticsearch: Smart Search for E-commerce in 2025
Learn how to integrate Elasticsearch with Laravel, from setup and configuration to indexing. Improve your app's search performance using Laravel Elasticsearch.
ScaleupAlly Team
Jul 3 ,
15 min read
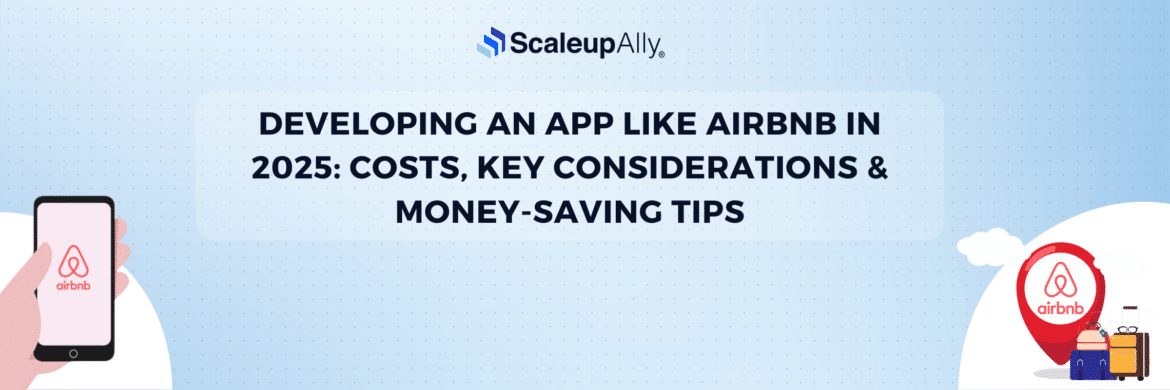
Developing an App Like Airbnb in 2025: Costs, Key Considerations & Money-Saving Tips
Discover the cost to build an app like Airbnb, key factors, app types, and smart ways to optimize development expenses for better ROI.
Suprabhat Sen
Jun 29 ,
10 min read
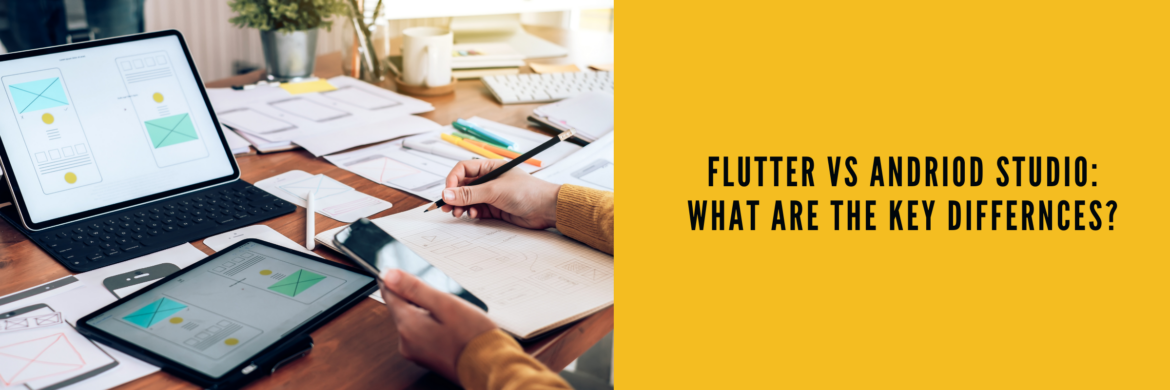
Flutter vs Android Studio: What are the Key Differences?
Flutter vs Android Studio: Wondering which technology to choose to build your next app. Here is a detailed guide that will help you make a decision.
Suprabhat Sen
Jun 28 ,
14 min read